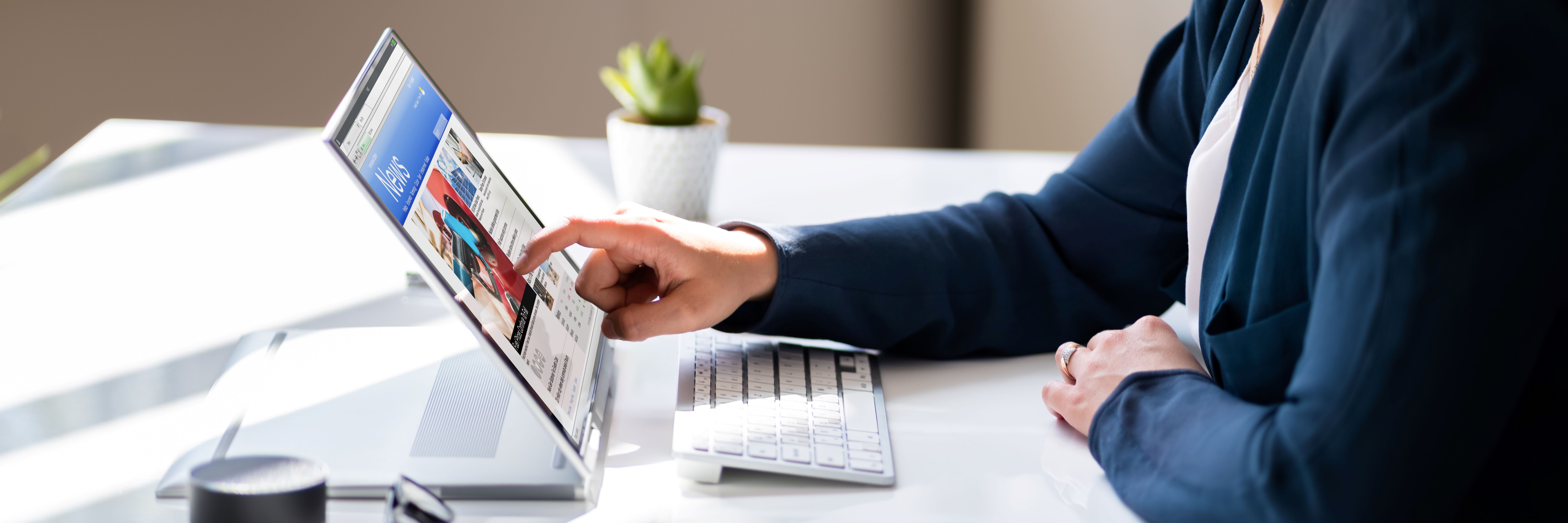
Visual Inspection Guide for Electronic Components
Thorough visual inspection is crucial for quality assurance of electronic components, especially upon initial receipt of materials. This type of inspection, conducted under a microscope, can precisely identify any surface or structural defects that may affect component functionality. Microscopic examination not only aids in identifying visual defects but also verifies the dimensional accuracy and correct positioning of components.
Choosing a Microscope
This microscope provides three-dimensional images, allowing operators to better perceive the surface structure of components. It is ideal for inspecting the physical integrity of electronic components, such as bent pins or defects in chip packaging. Stereo microscopes have a long working distance, allowing adjustments or movements of components without contact.
Microscope Settings
Light Source Type and Adjustment
● Direct and Transmitted Light: Direct light is suitable for observing surface details, commonly used in metallographic microscopes. Transmitted light is ideal for viewing internal structures, with the light source shining from beneath the sample.
● Polarized Light Source: Using polarized light can enhance the image contrast of certain materials, especially when observing metallic or some plastic components that reflect light.
Magnification and Resolution
The choice of magnification should be based on the size of the inspection target and the level of detail required. High magnification is used for examining micro defects but limits the field of view. Typically, start at a lower magnification to identify areas of interest, then switch to higher magnification for detailed observation.
Focus and Depth Control
Focusing is a critical step in microscopic observation, requiring accurate focus to achieve clear images. Depth control is especially important for thick samples or uneven surfaces, and proper adjustment ensures clarity across the entire field of view.
Sample Preparation
Before conducting a microscopic examination, ensure the sample surface is clean and dust-free. If necessary, gently clean the surface with appropriate cleaning agents and a soft brush to avoid introducing new defects or damage.
Inspection Strategy
● Systematic Inspection: Establish a fixed order of inspection, such as starting with labeling and numbering and gradually moving to more detailed checks like pin and packaging types, to systematically cover all key quality parameters.
● Record and Track: Thoroughly document the inspection results of each batch, including defect types and frequency. This data is valuable for tracking quality trends and assessing supplier performance.
Through these detailed settings and operational steps, microscopic inspection can provide solid support for the quality assurance of electronic components, thereby reducing the failure rate during production and enhancing the reliability of final products.
Visual Inspection Process
Visual inspection is a critical step in ensuring electronic components meet quality standards. Here is a detailed introduction to the visual inspection process, including professional execution methods and precautions for each step:
Verification of Marking and Numbering
● Check Markings and Numbering: Confirm that the markings and numbering on the components match the technical specifications or order requirements. This step ensures the received components are exactly what was ordered, avoiding the use of incorrect or counterfeit products.
● Inspect Clarity: Use magnification tools to check the clarity and integrity of markings. Any smudging, blurring, or errors could indicate issues during handling or quality control mistakes.
Pin and Contact Point Inspection
● Pin Alignment: Observe whether the pins are neatly aligned; uneven alignment can cause connection problems during assembly.
● Physical Damage: Check for bent, broken, or corroded pins, common causes of functional failures.
● Surface Condition: Inspect the pin surfaces for solder splashes, oxidation, or areas without plating, which could affect electrical performance.
Package Type Verification
● Dimension and Type Confirmation: Verify the type and dimensions of the packaging by comparing them with specification data.
● Package Integrity: Check for cracks, scratches, or other mechanical damage to the packaging. External damage could affect the integrity and functionality of the internal circuits.
Surface Defect Detection
● Inspect Surface Defects: Carefully examine the surface of electronic components for scratches, stains, or burns.
● Coating Uniformity: Observe whether the coating is evenly applied; uncovered areas could expose circuits to environmental elements.
Defect Recording and Data Management
● Record Defects: Detail all detected defects, using the microscope's camera function to take high-definition pictures; these images and data will serve as evidence for quality control.
● Data Entry: Enter inspection results into the quality management system in detail, including the date of inspection, operator, inspection equipment, and a detailed description of defects.
● Defect Categorization: Categorize defects based on their severity. Minor issues might be resolved through rework, while serious problems may require return or replacement.
Continuous Improvement and Supplier Feedback
● Evaluate and Adjust Inspection Processes: Regularly evaluate the effectiveness of inspection processes, adjusting the focus or techniques based on the types of problems found and their frequency to enhance the efficiency and accuracy of inspections.
● Supplier Feedback: Share statistical analysis results and improvement suggestions with suppliers to collaboratively enhance product quality and ensure quality control at every link in the supply chain.
These visual inspection processes systematically identify and record potential problems in electronic components, providing accurate data support for production and purchasing decisions while driving continuous improvement among suppliers to collectively enhance overall product quality and reliability.
By adopting a professional and systematic microscopic inspection process, it is possible to effectively ensure electronic components meet strict quality standards at the incoming stage. The judicious selection and setting of microscopes, along with detailed visual inspection methods, not only help identify surface and structural defects but also verify the dimensional accuracy and functional reliability of components. Through comprehensive checks of markings, pins, packaging, and surface defects, combined with defect recording and data management, a closed-loop quality control system can be formed.
In this process, professional testing and verification service providers like Rapid Rabbit can provide critical support. Rapid Rabbit focuses on testing and authenticity verification of electronic components, ensuring each batch of components undergoes rigorous inspection to meet the highest quality standards. Introducing Rapid Rabbit's services not only significantly reduces the failure rate during production but also enhances the performance and customer satisfaction of final products.