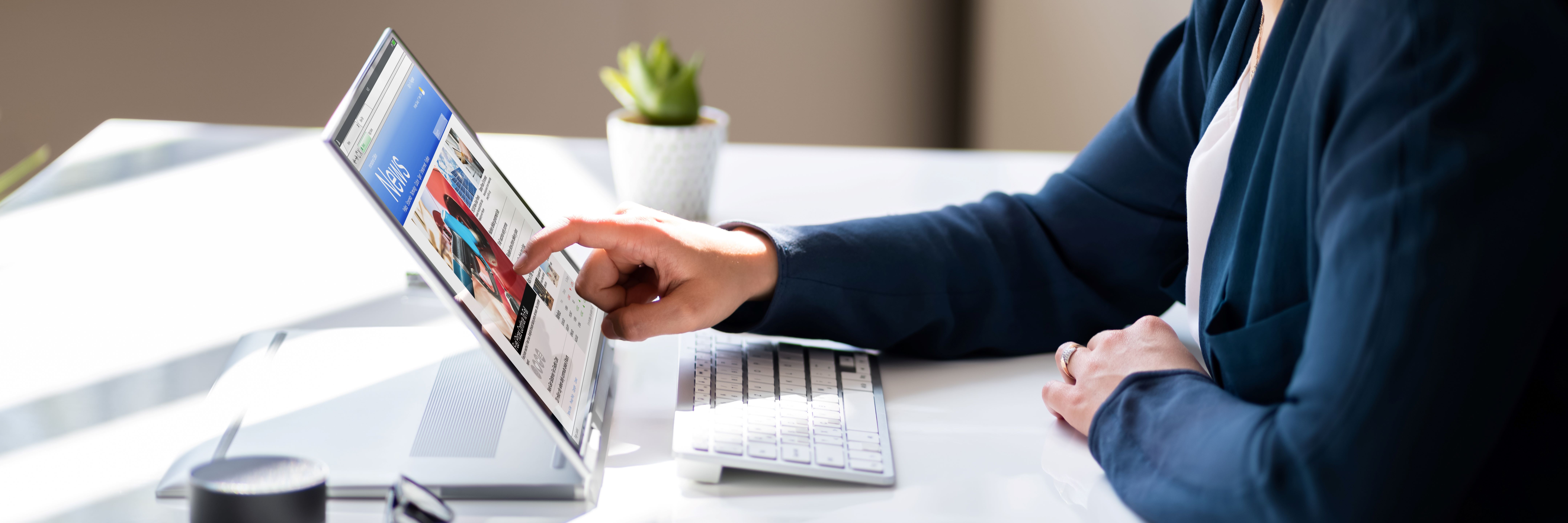
The 5 Hidden Killers Threatening Component Field Reliability
In the pursuit of smaller, faster, and more integrated electronics, engineers face a growing challenge: ensuring real-world reliability in the presence of complex and often invisible stress factors. While conventional testing can verify functionality under standard conditions, many failure mechanisms arise only during actual field use. Electrostatic discharge, thermal shock, humidity, mechanical stress, and electrical overstress (EOS) have become the silent threats behind premature system failures. This article outlines how these stressors impact modern components and what can be done to mitigate them.
Five Hidden Threats to Field Reliability
Among the most insidious is electrostatic discharge (ESD). A sudden burst of high voltage—even lasting just a few nanoseconds—can penetrate thin oxide layers, damage I/O protection circuits, and degrade performance over time. In practice, a USB interface might pass all initial tests, yet slowly fail after repeated ESD strikes, as signal quality deteriorates invisibly until functional collapse. Without robust protection circuits and proper ESD classification (such as HBM/CDM), these issues remain latent risks.
Thermal shock arises when components are exposed to abrupt temperature swings, such as during power cycling or environmental shifts. Inadequate thermal matching between materials can cause microcracks in solder joints or delamination between layers. BGA packages are particularly vulnerable; without sufficient thermal cycling validation, seemingly stable products may fail weeks into deployment.
Moisture and humidity introduce slow, penetrating damage. Water vapor can compromise package insulation, trigger metal ion migration, and lead to internal corrosion or dielectric breakdown. Failures often surface long after production—in the form of voltage drift, random resets, or short circuits. Cases like the "popcorn effect" in ceramic capacitors illustrate how environmental exposure quietly undermines stability.
Mechanical stress, whether introduced by pick-and-place machines, shipping vibration, or board flexing, tends to cause structural fatigue or displacement. These do not always result in immediate malfunction but often lead to performance degradation or intermittent faults later in life. Fragile components like MLCCs are especially susceptible when layout and support structures are overlooked.
Finally, electrical overstress (EOS) presents a serious threat at the system level. Unlike ESD, which is brief and sharp, EOS can last milliseconds or longer, carrying greater energy. Power surges, misplugged cables, or inductive spikes can destroy protection circuitry, melt interface pads, or corrupt logic registers. These failures are difficult to anticipate without simulating real-world usage conditions.
Strategies for Prevention and Validation
To combat these hidden killers, a multilayered approach is essential. Design teams should incorporate early-stage modeling to predict stress propagation—especially for thermal and mechanical effects. Selecting robust packaging materials and applying stress-tolerant layout practices greatly reduce the chance of latent failures.
Testing must extend beyond simple pass/fail checks. Standards like JEDEC JS-001/002, JESD22-A104/A105, and IEC 61000-4-5 offer validated protocols for simulating ESD, thermal cycling, humidity exposure, and surge events. However, real assurance comes from integrating these tests into application-specific validation workflows, often with the help of third-party labs.
Organizations such as Rapid Rabbit specialize in tailoring stress validation strategies to specific products, industries, and use cases. Their services help identify weak points early, simulate worst-case conditions, and deliver actionable data for risk-informed decision-making—an increasingly critical advantage in competitive, quality-driven markets.
Modern electronics are no longer tested merely for performance—they are tested for endurance. The greatest reliability threats are rarely visible in standard qualification, but they reveal themselves in the field, where ESD accumulates silently, solder joints fatigue over time, and voltage surges strike without warning. To build lasting products, manufacturers must address these subtle but potent forces with equal rigor.
In the end, reliability is not just about how well a component works on day one—it’s about how confidently it performs on day one thousand.