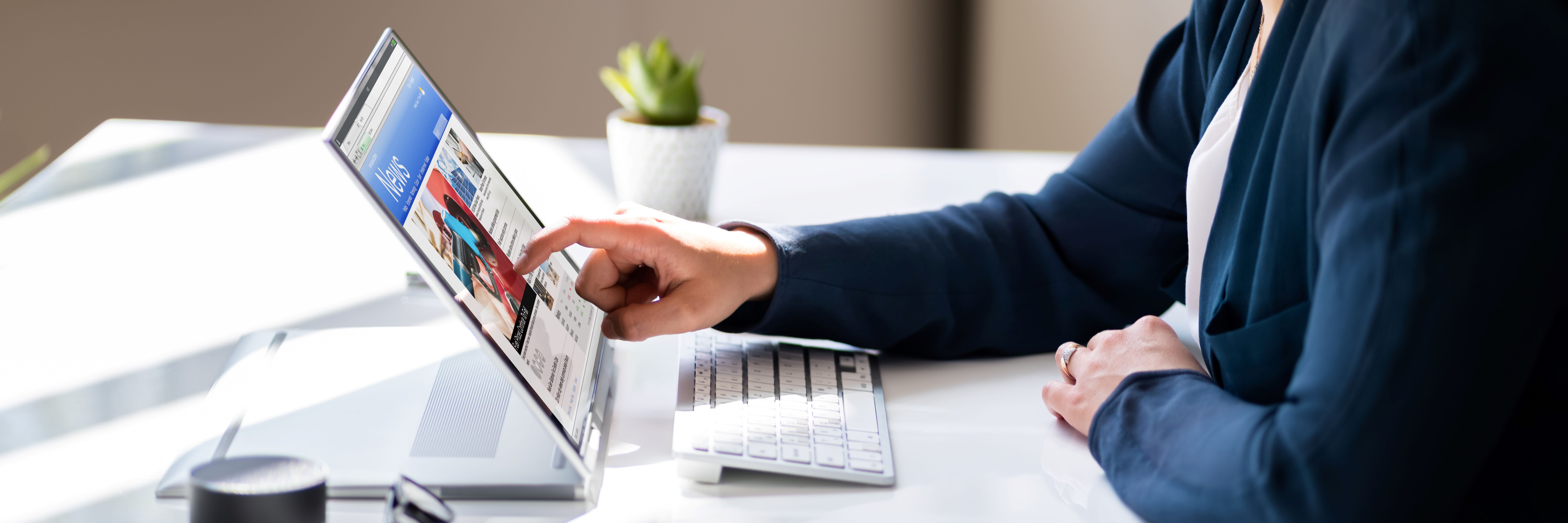
X-Ray Inspection for Reliable Components
Revealing the Hidden Risks of Packaging Defects
In modern electronics manufacturing, packaging processes—ranging from solder deposition and die attach to reflow soldering and molding—can introduce microstructural defects that are subtle yet critical. Unlike intrinsic circuit failures, packaging defects are often induced by material mismatches, thermal stress, mechanical strain, or soldering inconsistencies. Their concealed nature and delayed manifestation make them particularly dangerous, as they often evade visual and functional inspection but emerge under field conditions such as thermal cycling, humidity, or vibration.
Typical packaging defects include voids, head-in-pillow solder, solder collapse or bridging, delamination, underfill voids, and flux residues. Despite their low occurrence rates, these defects have a disproportionately high impact on long-term reliability, with studies attributing over 40% of system-level field failures to packaging-related structural anomalies. Detecting these issues with high precision and consistency is critical to achieving quality assurance in high-reliability manufacturing.
X-Ray Imaging: Principle and Capabilities
X-Ray inspection leverages the varying absorption rates of different materials to generate grayscale projection images, revealing hidden structures within opaque encapsulation layers. In a standard setup, an X-ray source emits radiation through the device, which is then captured by a detector. Materials like solder or copper absorb more X-rays and appear darker, while voids or low-density resins appear brighter.
Modern systems offer multiple imaging modes. 2D transmission imaging is ideal for high-throughput inspection, while oblique viewing enables angled imaging to better assess BGA collapse or central pad solderability. 3D CT (Computed Tomography) reconstructs volumetric models of the component from multiple angles, offering advanced insights into void distribution, delamination, and crack propagation—essential for failure analysis or high-precision diagnostics.
X-Ray not only visualizes solder joints and internal structures but also supports automated measurements of void ratios, solder coverage, ball deformation, and die attach quality. Integrated with barcode scanning and MES connectivity, X-Ray equipment becomes an intelligent probe embedded into the production line—capable of performing first article validation, sampling inspection, final quality checks, and returned goods analysis in a closed-loop framework.
Application Scenarios Across Key Packaging Types
In BGA and μBGA packaging, X-Ray is widely used to detect missing balls, bridging, excessive voiding (often limited to <25% per IPC-7095, or <10% for power-critical nodes), and misalignment. Advanced systems can automatically locate each solder ball, quantify voids, and log defects to enable traceability across production lots.
For QFN and LGA packages, where central thermal and ground pads dominate the structure, X-Ray provides detailed insights into paste coverage, voids under the center pad, and solder wettability on the perimeter pads. Oblique or layered imaging is particularly useful here, with some systems capable of simulating cross-sectional views that resemble C-SAM outputs.
In complex multi-die structures like PoP, SiP, or 3D ICs, CT imaging enables engineers to assess bonding between stacked dies, detect micro-bump shorts or opens, and evaluate filler distribution. This is critical in high-density modules like AI chips, camera processors, or DDR5 memory, where failure mechanisms can span multiple layers and interfaces.
In power packages such as TO, DPAK, or DFN, the emphasis shifts toward thermal and electrical continuity. X-Ray identifies voids in the die attach region, evaluates the quality of the main thermal path, and examines bond wire position and orientation. These analyses are indispensable in applications like EV inverters, power modules, and industrial converters.
Engineering Integration and Quality Control
The true power of X-Ray lies not just in visualization but in actionable interpretation. Standardization is essential: thresholds for void ratio, collapse depth, or misalignment should be set based on IPC-A-610 or IPC-7095 guidelines. Automated software now allows for real-time defect classification, image-based pass/fail judgment, and integration with MES systems for batch traceability. When combined with AOI and SPI systems, X-Ray becomes part of a comprehensive, multi-point inspection strategy that elevates both detection coverage and diagnostic accuracy.
X-Ray is rapidly transitioning from a stand-alone quality check to a key pillar of smart manufacturing. It forms the “perception layer” of intelligent production systems, capable of feeding visual and metric data upstream to enable predictive quality and process optimization.
Looking Forward: Higher Resolution, Greater Intelligence
X-Ray technology is moving toward higher resolution (down to 1–2µm or sub-micron), enabling wafer-level analysis and Chiplet structure verification. Inspection speeds are increasing to match the pace of SMT lines. Compact desktop CT systems are making advanced imaging more accessible. AI-driven defect recognition platforms are being built to support standardized image interpretation across regions and lines. Moreover, hybrid inspection approaches—combining X-Ray with thermal imaging, C-SAM, or OCT—are enabling multi-modal diagnosis of complex failure modes.
As the industry shifts from post-process repair to in-line quality prediction, X-Ray is evolving from a “corrective tool” to a “preventive system.” It is no longer just about seeing through packaging—it’s about knowing what lies beneath and acting before failures occur.
Packaging defects may be invisible to the naked eye, but their consequences are anything but. X-Ray inspection—thanks to its non-destructive nature, deep penetration, and quantifiable accuracy—has become indispensable across the electronic manufacturing lifecycle. From SMT validation and process quality control to advanced failure analysis and component reuse, X-Ray ensures every solder joint, every bond line, and every layer is accounted for.
For manufacturers and distributors alike, leveraging professional X-Ray testing services from providers like Rapid Rabbit not only enhances delivery confidence but also reinforces trust with customers by offering verifiable, traceable, and auditable quality proof points. In the age of reliability-driven design and zero-defect expectations, X-Ray is more than a tool—it’s the visual backbone of quality assurance.