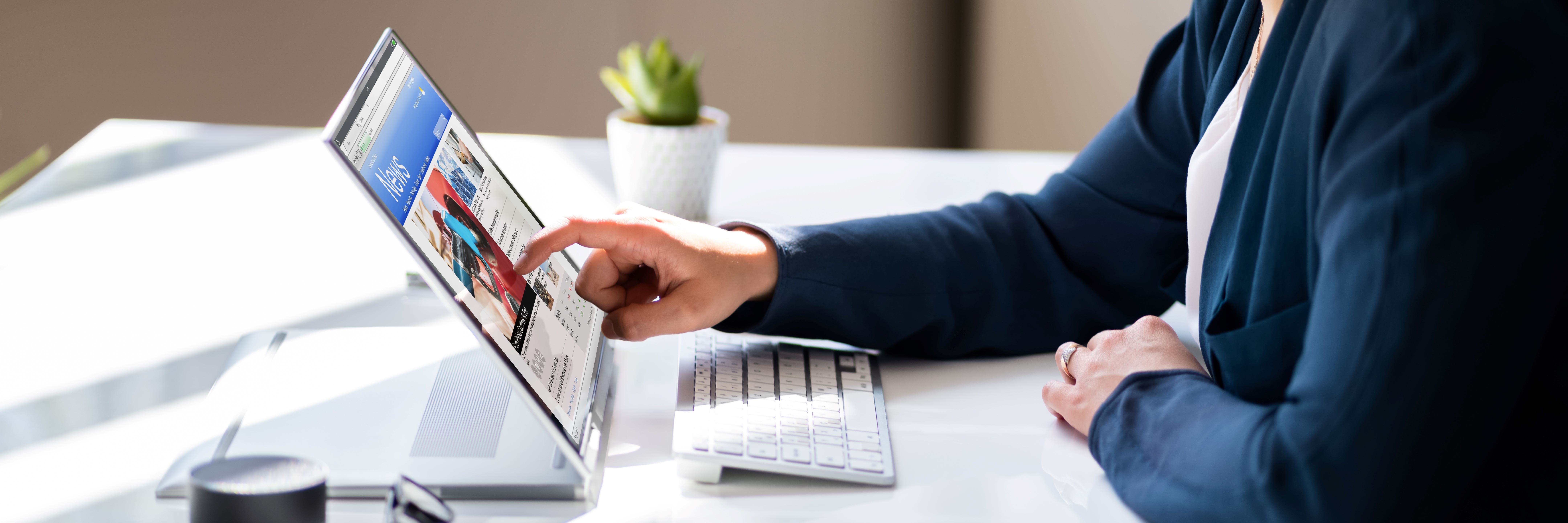
Thermal Reliability in IGBT & MOSFET Testing
As modern power electronics continue to advance at high speed, power devices such as IGBTs and MOSFETs have become central switching elements across key applications including renewable energy systems, electric vehicles, and industrial automation. With the growing demand for higher power density, these devices are required to operate under increasingly extreme conditions—high current, high voltage, and high switching frequency—all of which contribute to substantial heat generation. Thermal management has become a critical bottleneck for maintaining device stability and extending operational lifetime. Accurate characterization and control of thermal behavior is therefore fundamental to ensuring the performance, reliability, and safety of power electronic systems. However, the complex thermal dynamics of these components, combined with the challenges of precise testing, have made thermal management one of the most critical technical issues for engineers and test professionals alike.
1. Thermal Characteristics and Failure Mechanisms of Power Devices
Power devices inevitably generate heat during operation, mainly from conduction and switching losses. Conduction losses arise when the device is in the ON-state and current passes through internal channels—these losses are determined by saturation voltage (for IGBTs) and by the temperature-dependent on-resistance R<sub>ds(on)</sub> (for MOSFETs). Switching losses, meanwhile, occur during transitions between ON and OFF states, as voltage and current temporarily overlap. In high-frequency systems, these losses can become dominant, especially when tail current effects (in IGBTs) or output capacitance (in MOSFETs) are significant.
Excessive temperature rise within the chip leads to several failure modes. Localized hotspots, often caused by uneven current distribution across the silicon die, can result in electromigration or even localized breakdown. Solder fatigue and cracking in die attach layers or solder balls can degrade heat conduction efficiency and cause eventual device failure. Package delamination—arising from differential thermal expansion in molding compounds—further increases thermal resistance and can trigger mechanical failure. Additionally, thermal interface materials (TIMs) such as thermal greases tend to degrade under prolonged high temperature and pressure, further compromising heat dissipation.
2. Thermal Testing Challenges
Thermal dynamics in power devices are fast and non-linear, particularly under high-frequency switching. Junction temperatures can fluctuate significantly within microseconds, making traditional sensors like thermocouples unsuitable due to their limited speed and placement precision.
To overcome this, modern test methods increasingly rely on Temperature Sensitive Electrical Parameters (TSEPs), such as V<sub>CE(on)</sub> or R<sub>ds(on)</sub>, which exhibit predictable variation with temperature. These parameters allow indirect inference of junction temperature, but require accurate pre-characterization under controlled conditions to establish reliable calibration curves. While infrared (IR) thermography offers non-contact surface temperature mapping with good temporal resolution, variations in emissivity and radiation properties can introduce errors—requiring heat conduction models to extrapolate internal junction temperatures.
Advanced optical techniques, which use localized optical emissions to detect transient temperature changes, offer even higher spatial and temporal resolution, making them ideal for capturing rapid thermal events.
Test conditions themselves significantly affect thermal measurement accuracy. Heat sink structure, TIM thickness and uniformity, contact pressure, and substrate material all contribute to variability in thermal resistance measurements. Therefore, test fixtures must be standardized—using uniform heatsinks, consistent TIM application, and stable mechanical loading to minimize variability and ensure repeatability. Given that heat flows through complex paths from chip to heatsink—via die attach, solder layers, and copper substrates—even slight differences in any layer can affect results. Furthermore, variations in ambient airflow or cooling conditions (air vs. liquid) add complexity to test environments.
To address these challenges, engineers often construct detailed thermal equivalent circuit models, validate them through a combination of simulation and empirical data, and implement multi-point temperature sensing—often assisted by thermal imaging—for comprehensive system-level thermal analysis.
3. Key Thermal Parameters and Measurement Techniques
The junction temperature (T<sub>j</sub>) is a core metric in evaluating thermal performance and directly determines both safe operating area and device longevity. Due to the physical inaccessibility of the junction, indirect measurement is standard practice. Electrical parameters like V<sub>CE(on)</sub> or R<sub>ds(on)</sub> are used to estimate T<sub>j</sub> by referencing pre-established calibration curves. Combined with thermal imaging and multiphysics modeling, these approaches can provide reliable estimations even under dynamic or pulsed operating conditions.
Pulse-based thermal measurement is particularly effective for assessing transient thermal behavior. By applying a known current or voltage pulse and measuring the resulting temperature rise over time, engineers can reconstruct thermal response curves. These methods are vital for capturing dynamic temperature behavior under realistic switching loads.
Thermal resistance (R<sub>th</sub>) is another crucial metric, describing how effectively heat is transferred through materials. Commonly evaluated values include junction-to-case (R<sub>th(j-c)</sub>), junction-to-ambient (R<sub>th(j-a)</sub>), and junction-to-test-point (R<sub>th(j-t)</sub>). These are typically determined using standardized procedures such as those in IEC 60747. Thermal capacitance (C<sub>th</sub>) reflects the energy required to induce a given temperature change and influences the rate of thermal response—devices with higher thermal capacitance can absorb short-term thermal spikes, but may also retain heat longer, increasing cumulative thermal stress.
4. Techniques and Equipment for Thermal Testing
Pulse testing methods are widely used to characterize transient heating behavior and validate the effectiveness of heat dissipation structures. Dynamic thermal impedance testers—such as the T3Ster system—enable layered thermal path analysis, distinguishing individual contributions to total thermal resistance and identifying specific thermal bottlenecks.
Thermal cameras, when synchronized with electrical waveform capture via oscilloscopes, enable simultaneous observation of electrical and thermal behavior. This dual-domain insight is invaluable for understanding failure mechanisms and optimizing layout or packaging strategies.
Proper thermal testing spans the entire lifecycle of a power device—from material selection and structural design to testing and in-field operation. Accurate thermal evaluation not only ensures immediate reliability but also supports predictive maintenance, robust failure analysis, and long-term performance assurance.
Thermal management is a foundational challenge in the reliable deployment of modern power devices. From transient heating during high-speed switching to material degradation over long-term cycling, understanding and controlling thermal behavior is essential. As power systems evolve to higher densities and stricter reliability targets, manufacturers must embrace both precision measurement and holistic thermal design.
By leveraging cutting-edge thermal testing workflows—and collaborating with expert partners like Rapid Rabbit—engineers can build confidence in their thermal models, identify risks early, and secure long-term product performance. In an era driven by electrification and energy efficiency, those who master thermal control will lead not only in engineering precision but also in market success.