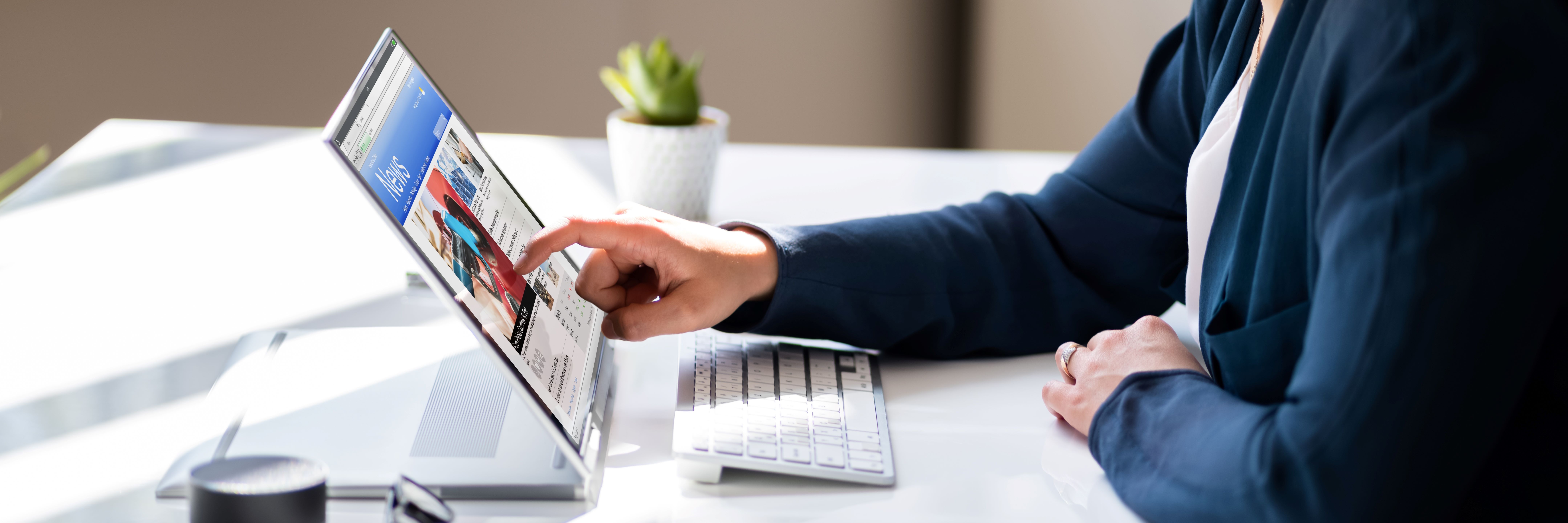
ESD Testing and the Reliability of Electrostatic-Sensitive Components
As electronic products evolve toward greater miniaturization, integration, and intelligence, electrostatic discharge (ESD) has become an increasingly critical factor affecting the performance and reliability of electronic components. ESD is not only a common cause of component failure—it can also lead to temporary system malfunctions, long-term performance degradation, or even complete device breakdown. Particularly for high-frequency, high-density, and sensitive components such as semiconductors, sensors, capacitors, and resistors, the threat posed by ESD is especially severe.
This article explores the role of ESD testing in the electronics industry, evaluates its impact on the reliability of sensitive components, and outlines key strategies—including design optimization and robust testing—to improve ESD immunity and overall system resilience.
I. Understanding Electrostatic Discharge (ESD) and Its Hazards
Electrostatic discharge (ESD) is the sudden flow of electric current between two objects with different electric potentials, either through direct contact or proximity. Due to their microscopic structures and ultra-fine geometries, electronic components are especially vulnerable to this phenomenon.
Key Hazards of ESD:
●Direct Damage: ESD can involve voltages of several kilovolts or even tens of kilovolts, and peak currents reaching several amperes—sufficient to destroy internal structures. For example, the gate oxide of a MOSFET may rupture, or IC metal traces may melt, resulting in permanent failure.
●Functional Failure: ESD can impair functionality even without causing immediate, visible damage. Subtle electrical stress may result in long-term parameter drift, affecting system performance and stability over time.
●Data Loss and System Crashes: Memory devices such as DRAMs and HDDs are prone to data corruption or signal interference caused by ESD, potentially leading to operating system errors or application-level failures.
●Intermittent Failures: Some components may initially appear unaffected but develop sporadic issues over time, particularly under thermal or voltage stress. These latent faults are difficult to detect and pose long-term reliability risks.
II. ESD Sensitivity Across Component Types
Different types of electronic components exhibit varying levels of ESD sensitivity, with distinct failure modes depending on their structure and application. Below is a breakdown of ESD effects by component category:
1. Semiconductor Devices
Semiconductors, especially integrated circuits (ICs), are among the most ESD-sensitive components.
●MOSFETs: The gate oxide layer, often only tens of nanometers thick, is highly susceptible to dielectric breakdown from ESD, leading to gate-to-source shorts and functional failure.
●BJTs (Bipolar Junction Transistors): ESD can induce junction breakdown, affecting gain characteristics and potentially resulting in open or short circuits.
Testing Standards: Common semiconductor ESD tests follow IEC 61000-4-2 or ANSI/ESDA/JEDEC JS-001, simulating various discharge levels to determine device breakdown thresholds.
2. Sensors and MEMS Devices
Sensors and MEMS components often contain delicate capacitive or resistive structures, making them highly vulnerable to ESD-induced failure.
●Accelerometers, pressure, and humidity sensors: Tiny embedded capacitors or mechanical structures can be damaged by ESD, altering readings or causing full failure.
●MEMS gyroscopes: Relying on precise micromechanical motion, these are easily disrupted by discharge events, reducing sensitivity or rendering them non-functional.
3. Passive Components (Resistors, Capacitors, Inductors)
Passive components are generally more resilient but not immune—especially in high-frequency or high-voltage applications.
●Capacitors: Sudden voltage spikes may damage the dielectric material, especially in ceramic capacitors, resulting in reduced capacitance or short circuits.
●Resistors: High-voltage ESD may cause localized heating and material degradation, leading to resistance shifts and instability.
4. Optoelectronic Components
Optoelectronic devices such as photodiodes, LEDs, and fiber-optic sensors can experience ESD-related degradation in optical output or signal integrity, compromising data transmission and system performance—particularly in telecom applications.
III. ESD Testing Standards and Methodologies
To mitigate the risks posed by static electricity, various international standards have been developed to evaluate ESD immunity under controlled conditions.
Common Standards:
●IEC 61000-4-2: The most widely used standard for ESD immunity, covering contact and air discharge simulation across a range of voltage levels. Applicable to general-purpose electronics.
●ANSI/ESDA/JEDEC JS-001: Focused specifically on semiconductor device sensitivity, specifying pulse waveforms, current limits, and test setups for component-level qualification.
●MIL-STD-883: Designed for military and aerospace applications, this standard imposes stricter environmental conditions (high temperature, humidity, vibration) and extreme ESD thresholds.
IV. Strategies to Improve ESD Immunity
To enhance the robustness of sensitive components against ESD threats, design engineers and manufacturers adopt a combination of the following strategies:
●Shielding and Grounding: PCB layout should include proper grounding schemes and EMI shielding to safely divert ESD energy away from critical circuitry.
●Use of ESD Protection Devices: Transient Voltage Suppression (TVS) diodes, clamping diodes, and integrated protection circuits are employed to absorb and neutralize ESD pulses.
●Package Optimization: Selecting packaging materials and designs that offer higher dielectric strength can improve a component’s intrinsic ESD resistance.
●Comprehensive ESD Testing: Component-level tests should be integrated into the validation process to ensure resilience in real-world handling, transport, and operational scenarios.
V. ESD Testing as a Core Reliability Practice
As components become smaller and more sensitive, ESD testing has become indispensable for ensuring both short-term functionality and long-term reliability. Rigorous testing and robust design not only prevent device damage but also enhance system stability and safety.
With increasing global demands for product reliability and regulatory compliance, ESD testing is now a competitive differentiator. It enables manufacturers to build stronger brands and deliver consistent performance under real-world conditions.
By partnering with professional testing laboratories like Rapid Rabbit, companies gain access to standardized, high-accuracy ESD assessments. These third-party services help manufacturers mitigate the risks of electrostatic damage across production, logistics, and field use—ultimately strengthening their ability to meet modern reliability expectations and win in competitive markets.
In an era where electronic systems are more complex and mission-critical than ever before, ESD resilience is no longer optional—it is a core competency. With the support of AI-driven testing methods and expert testing partners, the industry is moving toward a future where reliability, transparency, and electrostatic protection form the foundation of sustainable innovation.