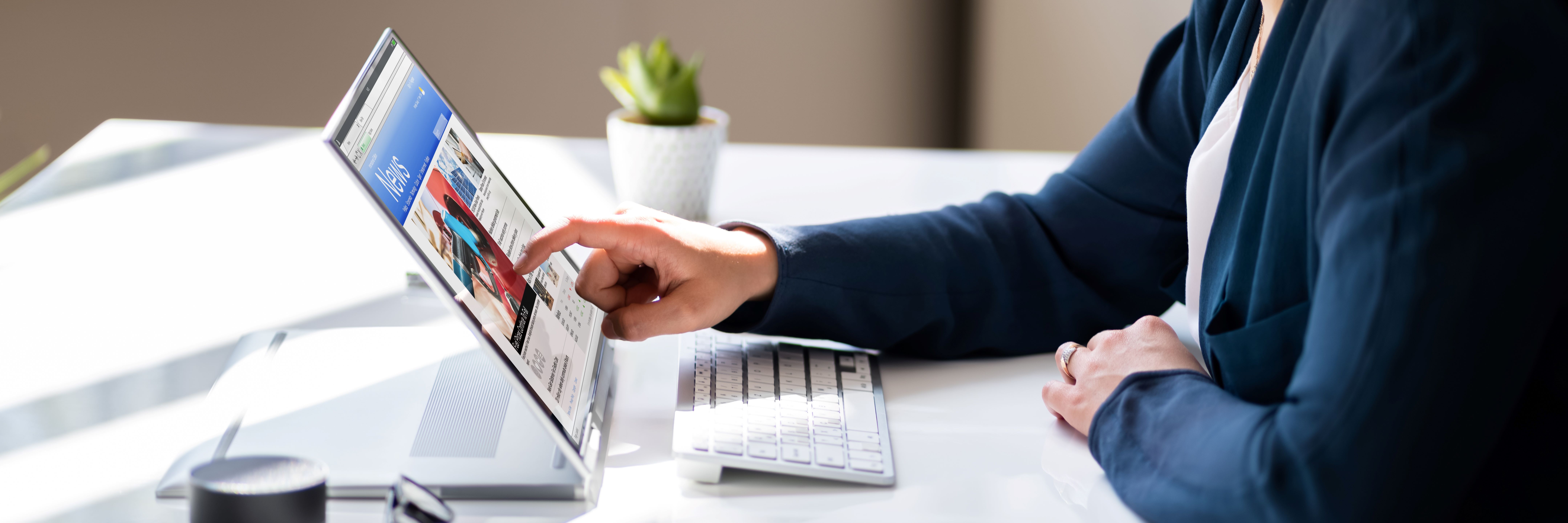
SMD Capacitor Testing
As one of the most widely used components in modern electronics, surface-mount capacitors (SMD capacitors) are essential for filtering, coupling, decoupling, and energy storage applications. With the increasing miniaturization of devices, rising power densities, and higher operating frequencies, precise performance testing of capacitors has become more critical than ever. In high-frequency and high-precision circuit designs, the quality and stability of capacitors directly affect overall system reliability and performance.
However, testing SMD capacitors is far from straightforward—it involves accurate evaluation of multiple parameters including capacitance, equivalent series resistance (ESR), and breakdown voltage. Any deviation in these values can significantly impact device behavior. This article explores the key testing challenges and outlines comprehensive parameter management strategies to ensure stable and reliable capacitor performance across applications.
1. Capacitance Testing: The Core Metric
Capacitance defines a capacitor’s ability to store charge and is central to its function in electronic circuits. It determines the capacitor’s behavior in filtering, decoupling, and coupling roles. Accurate capacitance testing is essential, particularly in high-frequency designs where small deviations can affect system behavior.
1.1 Methods and Challenges
Common methods include the DC charge/discharge method and AC impedance response testing. For SMD capacitors used in high-frequency circuits, testing instruments must support high-frequency response, as capacitance values can shift at frequencies above 10 kHz due to parasitic inductance and ESR.
Low vs. High Frequency Performance:
At low frequencies, capacitance remains relatively stable. However, at higher frequencies, the effective capacitance can vary significantly due to parasitic elements. Accurate high-frequency testing must account for these effects.
Precision Demands:
As component sizes shrink and values reach the picofarad (pF) range, external noise, ambient conditions (temperature, humidity), and instrument error all influence test results. Precision equipment and controlled environments are essential for reliable measurements.
2. ESR Testing: A Key Indicator of Loss
Equivalent Series Resistance (ESR) represents the internal resistive losses within a capacitor. High ESR values lead to energy dissipation, heating, and degraded performance, especially in power supply filters and decoupling applications.
2.1 ESR Testing Methods
Low-Frequency Testing:
ESR is typically measured at 1 kHz or lower, where the resistive component dominates. Measurement involves applying an AC signal and analyzing the resulting voltage/current to derive the ESR value.
High-Frequency Considerations:
At higher frequencies, ESR becomes nonlinear and significantly affects signal attenuation. For RF and high-speed circuits, ESR testing must be performed using high-frequency-capable instruments like precision LCR meters.
2.2 Testing Challenges
Temperature Sensitivity:
ESR increases with temperature, especially under continuous high-load conditions. This impacts capacitor life and efficiency. Effective ESR testing should factor in temperature variations to simulate actual operating environments.
Measurement Precision:
Since ESR values in high-quality capacitors are extremely low, even small measurement errors can cause significant inaccuracy. High-resolution instruments and stable test setups are required for reliable ESR analysis.
3. Breakdown Voltage Testing: Understanding the Limits
Breakdown voltage defines the maximum voltage a capacitor can withstand without dielectric failure. Exceeding this threshold can result in short circuits or catastrophic failure, making it a crucial parameter for power electronics and high-voltage systems.
3.1 Testing Method
Breakdown testing involves gradually increasing voltage until the capacitor fails. Specialized equipment applies the rising voltage and monitors insulation failure or sudden current spikes to determine the breakdown point.
3.2 Testing Challenges
Batch Variability:
Even within the same production batch, breakdown voltage can vary due to process instability or raw material inconsistencies. Random sampling helps assess consistency and manufacturing quality.
Thermal Effects:
Breakdown voltage tends to decrease at elevated temperatures. Simulating real-world temperature conditions during testing is essential for accurate reliability assessments.
Capacitor Type Dependency:
Different capacitor types exhibit different breakdown characteristics. Electrolytic capacitors typically have lower breakdown voltages, while ceramic types may fail abruptly under thermal or voltage stress. Testing procedures must be tailored accordingly.
4. End-to-End Testing and Quality Management
Testing SMD capacitors is not just about measuring parameters but requires integrated quality control throughout the design, production, and shipping stages.
4.1 Design Phase
Establish clear selection criteria for capacitance, ESR, and breakdown voltage. Use circuit simulation tools to verify capacitor behavior under expected operating conditions and frequencies.
4.2 Production Phase
Ensure process consistency to meet design specs. Implement automated testing systems for in-line verification of capacitance and ESR, filtering out early-stage defects.
4.3 Final Testing and Reliability Control
Before shipment, conduct full validation including capacitance, ESR, and breakdown voltage testing. Complement these with reliability tests under high temperature, humidity, and voltage to evaluate long-term stability and aging behavior.
By combining accurate testing with robust process control, manufacturers can ensure that SMD capacitors meet the demanding requirements of today’s electronic systems. As performance thresholds rise with newer generation devices, the role of precise testing becomes increasingly critical.
Collaborating with professional testing service providers such as Rapid Rabbit enables enterprises to perform advanced diagnostics, catch hidden defects early, and ensure that every capacitor meets performance and safety standards. These third-party insights support both design validation and volume production, helping manufacturers maintain high quality, enhance reliability, and meet market expectations.
As testing technology continues to evolve, capacitors will become even more reliable and efficient—backed by increasingly precise testing and stronger quality control across the supply chain.