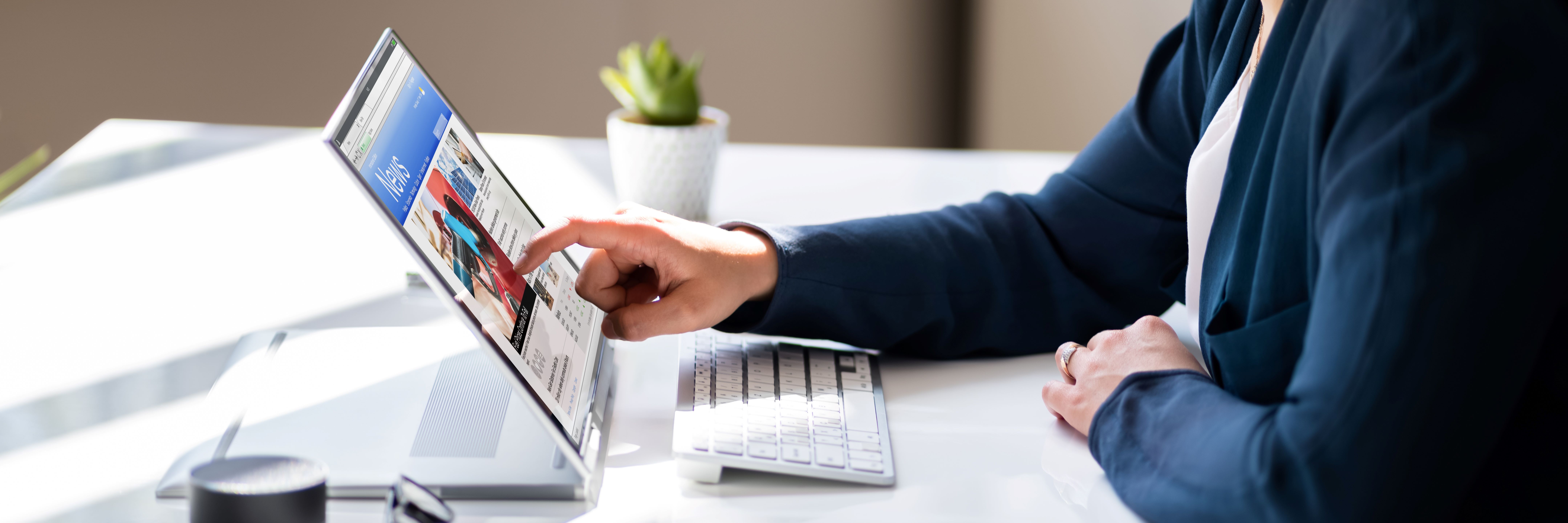
Theory and Practice of Thermal Cycling and Temperature Shock Testing
Thermal cycling and temperature shock testing are two crucial methods in verifying the reliability of electronic components. Thermal cycling primarily assesses the durability of components when exposed to prolonged temperature changes, while temperature shock focuses on the effects of sudden temperature changes. Both tests simulate the stresses caused by temperature fluctuations in real-world environments and rigorously validate the reliability of electronic components, especially in extreme applications such as automotive, aerospace, and military.
Physical Mechanisms of Thermal
Cycling and Temperature Shock Thermal Cycling
Formation of Thermal Stress: During thermal cycles, the materials and structures within electronic components expand and contract multiple times, generating thermal stress. This is particularly significant in components made from different materials (such as metal and ceramics or plastics) due to differing coefficients of thermal expansion, which can lead to microcracks at weld points and interfaces. These microcracks may expand with increasing numbers of thermal cycles, potentially leading to the detachment of solder joints, cracking of encapsulation materials, and fractures within internal structures. Thermal Fatigue: Thermal cycling tests essentially evaluate thermal fatigue of components, where repeated temperature changes cause material fatigue accumulation. Similar to other types of fatigue, such as mechanical fatigue, thermal fatigue can alter the microstructure of materials, ultimately leading to failure. For metals, long-term thermal cycles can disrupt interatomic bonds, reducing yield strength and eventually causing fractures.
Temperature Shock: Stress Concentration from Thermal Shock
Temperature shock tests typically subject components to rapid and extreme temperature changes. These swift changes can cause uneven thermal expansion among different parts, leading to stress concentration. This is particularly vulnerable at interfaces between high thermal conductivity materials (like metals) and low conductivity materials (like plastics or ceramics), where stress concentration areas are most likely to develop microcracks or even break. Stress and Structural Damage: The thermal stress induced by temperature changes can cause local plastic deformation in the structure of components, especially at solder joints or adhesive layers. During temperature shock tests, extreme temperature changes can quickly induce plastic flow or fractures in these areas.
Standards and Methods for Thermal Cycling and Temperature
Shock Testing Thermal Cycling Standards: Standards vary by industry. For instance:
AEC-Q100: A standard for automotive electronic components, requiring at least 1000 thermal cycles between -40°C to +125°C.
MIL-STD-202: A standard for military electronic devices, with temperature cycles ranging from -55°C to +125°C, the number of cycles depending on the specific project.
Testing methods typically set specific upper and lower temperature limits, with defined durations for each temperature stage. In some applications, the rate of thermal cycling is also standardized, such as a temperature change rate not exceeding 10°C per minute, or requiring rapid temperature changes to simulate quick startups and shutdowns.
Temperature Shock Standards: IPC/JEDEC-9702
A standard for consumer electronics temperature shock tests, requiring components to withstand rapid temperature changes from -40°C to +150°C, with shock durations ranging from a few seconds to several minutes. MIL-STD-810: A common standard in the military sector, requiring components to quickly adapt to extreme temperature shocks, such as a sudden change from -65°C to +125°C. Testing methods generally occur in thermal test chambers, rapidly switching between hot and cold sources to achieve swift temperature changes. Test equipment can usually transition components from one extreme temperature to another within a very short period (like within 1 minute), simulating sudden environmental temperature changes.
Analysis and Application
Impact on Component Performance
Thermal cycling and temperature shock can affect the solder joints and conductive connections of components. Especially in Surface Mount Technology (SMT) components, the reliability of solder joints is a key factor in component stability. Repeated thermal changes can gradually increase stress on the solder points, potentially leading to cracks or detachment, thereby affecting the functionality of components.
Encapsulation Material Performance
The encapsulation materials of components undergo changes in material properties during thermal cycling and temperature shock, such as delamination due to different thermal expansion coefficients and cracking of the encapsulation. Aging and fatigue of encapsulation materials not only affect the physical structure of electronic components but also their electrical performance, impacting long-term reliability.
Experimental Results Analysis
In practical testing, component performance data before and after temperature cycles, such as changes in electrical parameters (e.g., resistance, capacitance, signal quality), are compared to assess durability. Microscopic analysis (like Scanning Electron Microscopy) and X-ray inspections can help detect microstructural changes in solder points and encapsulations, further validating test results.
Thermal cycling and temperature shock tests are fundamental to verifying the reliability of electronic components under harsh conditions. By simulating real-world temperature variations, these testing methods not only help predict the lifespan of components but also reveal potential structural weaknesses, providing a theoretical basis for improvements and optimization of electronic components.
In these demanding testing processes, Rapid Rabbit, as a professional electronic component testing service provider, offers precise testing solutions. With its advanced testing equipment and extensive industry experience, Rapid Rabbit delivers comprehensive services, meeting the high standards of different clients for component performance in various environments.