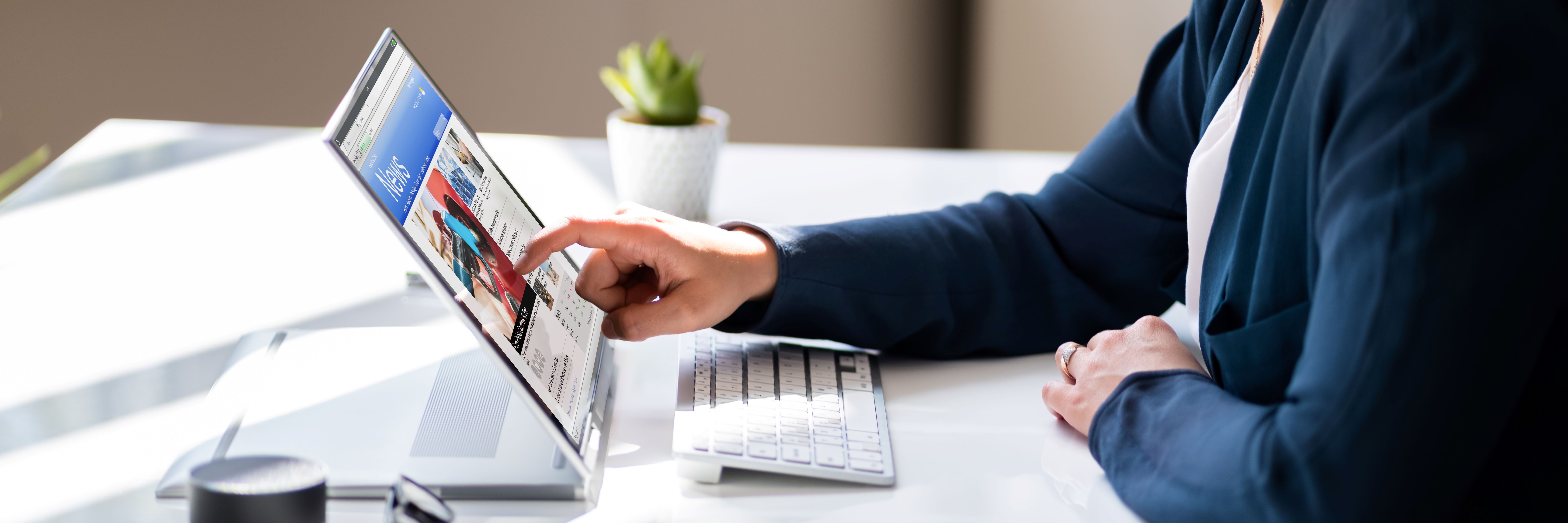
AI-Driven Testing of Electronic Components
In the highly competitive and rapidly evolving electronics industry, component testing has grown beyond its traditional role as a quality checkpoint. It is now a critical foundation for ensuring system stability and product safety. With increasing complexity in component types and usage scenarios, conventional testing methods are becoming inadequate in terms of efficiency, precision, and adaptability. The rise of artificial intelligence (AI) is quietly injecting new momentum into this domain.
From visual inspection and parameter modeling to failure prediction and trend forecasting, AI is redefining the boundaries of value in electronic component testing. This article explores three core applications of AI in the component testing workflow: defect identification, parameter fitting, and trend prediction.
Visual Intelligence: Reshaping Inspection with AI-Powered Image Recognition
Visual inspection has long been a bottleneck in component receiving, quality control, and shipping processes. Issues such as missing silkscreen, packaging defects, bent leads, and damaged solder balls have traditionally relied on manual judgment—often influenced by environment, fatigue, and subjectivity—leading to high miss rates, poor consistency, and low throughput.
With advances in AI vision, deep learning-based image recognition models—particularly convolutional neural networks (CNNs)—have been widely deployed in defect detection systems. These models can learn subtle differences between tens of thousands of standard and defect images, enabling accurate identification of complex flaws like counterfeit markings, micro-cracks, and BGA ball shifts.
In practical deployments, an AI-integrated inspection system can process high-density SMT images in just 0.1 seconds per frame, achieving over 95% accuracy, significantly outperforming manual inspection. These systems also support customizable inspection thresholds to match diverse quality requirements from different customers.
Data-Driven Insights: Enhancing Test Resolution with Parameter Fitting
Electrical parameter testing has always been central to component validation. However, conventional methods typically use static thresholds to determine pass/fail outcomes, often ignoring the non-linear behaviors of components under varying environmental conditions. AI introduces new possibilities by transforming discrete data points into continuous performance surfaces through regression modeling and feature analysis.
In practice, algorithms like support vector regression (SVR) and polynomial regression enable AI systems to model voltage, current, and frequency responses more precisely. This allows identification of components that appear nominal but exhibit systemic drift risk. For example, in high-temperature testing of MLCC capacitors, AI models can detect gradual capacitance degradation, proactively flagging components prone to latent failures.
Furthermore, for long-duration tests such as aging and thermal stress, AI time-series models like long short-term memory (LSTM) networks can predict future parameter trends, offering engineers quantitative tools to support decision-making. This shift from binary qualification to performance understanding is driving a deeper transformation in the testing paradigm.
Predictive Quality: Enabling Proactive Risk Control with AI
AI’s third major contribution lies in extracting value from massive, multi-variable test data sets. Historically, test data was treated as a byproduct of the acceptance process. Today, it is increasingly seen as a valuable asset for quality prediction.
By leveraging historical data to build predictive models, AI systems can:
●Forecast failure rate trends for specific suppliers or packaging batches over the next 3 months
●Identify degradation risks for specific models under high temperature, humidity, or voltage conditions
●Detect systemic drift in interface components due to process shifts in production lines
For instance, one testing service provider analyzed over 400,000 data samples using AI and uncovered a response time anomaly in a specific batch of power management ICs from a major brand. The alert enabled the client to revise component selection and avoid future recall losses. This proactive capability shifts component testing from static control to dynamic early warning, supporting smarter sourcing, qualification, and inventory strategies across the supply chain.
Bridging Challenges: Making AI Testing Practical and Scalable
Despite its clear benefits in accuracy, speed, and insight, implementing AI testing solutions still presents real-world challenges:
●Limited defect image samples for training, reducing model generalization
●Low interpretability of AI predictions, affecting user trust
●High integration barriers with legacy test equipment due to a lack of standard protocols
●Concerns around data privacy and regulatory compliance, especially when sensitive materials are involved
To overcome these hurdles, the industry is exploring emerging technologies such as few-shot learning, edge AI inference, and federated learning, aiming to enhance model robustness and adaptability in constrained environments.
From detecting micro-defects to modeling performance and predicting future risk, AI is transforming testing from a backend activity into a strategic function—from reactive checks to predictive insights, from operational tool to decision enabler. This shift reflects both technological advancement and the rising strategic importance of quality assurance in modern manufacturing systems.
As expectations grow for high reliability, rapid response, and traceable data, companies are increasingly turning to professional third-party testing partners. Among them, Rapid Rabbit, a specialist in electronic component testing, is establishing itself as a trusted bridge between distributors, OEMs, and end customers. With standardized procedures and responsive operations, Rapid Rabbit provides essential support for risk mitigation and quality verification.
In the era of increasingly complex and mission-critical electronics, testing is no longer the "visible end" of the process—it is the intelligent beginning. The convergence of AI-powered methods and independent testing expertise will shape a more transparent, efficient, and trustworthy component quality ecosystem.