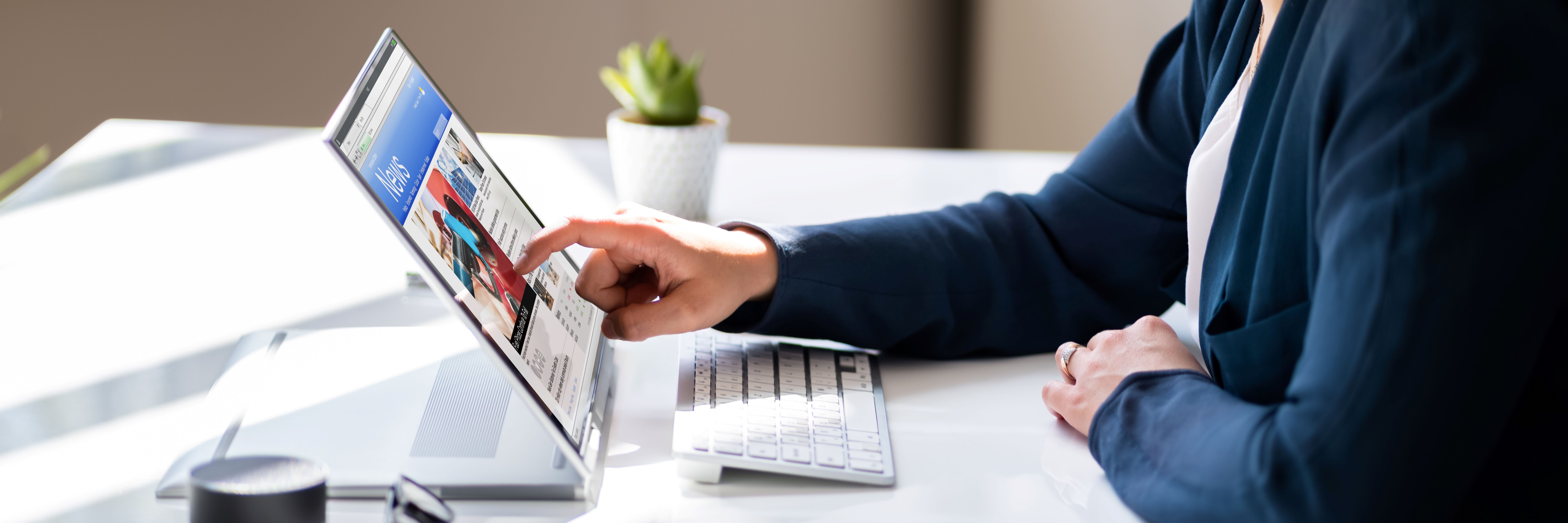
Applications of X-ray Analysis in Electronic Component Verification
In the electronics industry, X-ray analysis technology has become a key technique for ensuring component quality and consistency. This non-destructive inspection provides deep insights into the internal structures of electronic components, enabling highly precise quality control during the production process. This article will explore the specific applications of X-ray analysis in electronic component verification, covering the inspection of internal wafer structures, batch consistency assurance, and comparative analysis against specifications or known authentic samples.
Fundamental Principles of X-ray Technology
X-rays are a form of electromagnetic radiation with extremely short wavelengths, capable of penetrating most solid materials. In the electronics industry, X-rays are used to generate images of the internals of components, revealing details within the package such as wafers, pin connections, and solder joints. Because X-rays provide a clear internal view without damaging the sample, they are an ideal choice for assessing the integrity inside packages and conducting quality control.
Importance of Verifying Internal Wafer Structures
Wafers are the core part of most electronic components, and their structural integrity directly impacts the functionality and reliability of the components. X-ray technology allows engineers to examine the microstructures within wafers, including crystal arrangements, lattice defects, and potential internal fractures. Additionally, this technology is used to assess the alignment accuracy of wafers and the integrity of interlayer connections, which are critical factors affecting device performance.
Ensuring Batch Consistency in Components
Maintaining high batch consistency is a challenge and a necessity in the production of electronic components. X-ray analysis provides an effective method to inspect and confirm that batch components conform to design specifications. By analyzing X-ray images of different components, manufacturers can identify variations and deviations in the production process, such as misaligned pins, mislayered wafers, or uneven solder distribution, allowing for rapid corrective actions in mass production.
Analysis Comparisons Against Specifications and Real Samples
Comparing the X-ray images of electronic components with specifications or known authentic samples from the same batch is a crucial step in verifying product quality. This comparison can reveal any deviations from specifications, such as differences in material density, component layout, or internal structure. Furthermore, comparative analysis is also a critical method for identifying counterfeit components, as illegally replicated items often exhibit noticeable internal structural discrepancies.
Practical Case Study
In the manufacturing of high-performance microprocessors, the integrity of wafers is critical. These microprocessors are typically used in applications requiring high computational power and stability, such as data centers, high-end servers, and complex graphics processing. Any minor defects, such as internal voids in the wafer, can lead to severe performance issues.
During quality testing, X-ray analysis technology was used to perform a thorough internal structure inspection of the new generation of microprocessors' wafers. The analysis revealed unusual voids in the silicon substrate of the wafers. These voids appeared as a series of dark spots on the X-ray images, indicating a lack of necessary silicon material in critical areas of the wafer.
Voids within the wafer can disrupt the electronic pathways in the microprocessor, leading to instability in the electric current or overheating, which is particularly dangerous under high-load conditions. For example, during massive data processing or complex computational tasks, the affected microprocessors could experience performance drops or complete failures, impacting the overall system's stability and reliability.
After identifying the issue, a detailed analysis of the wafer growth and deposition processes was conducted. It was found that the formation of voids was linked to improper temperature control during the wafer growth process. To address this issue, adjustments were made to the temperature distribution and growth rate in the growth furnace, ensuring even deposition of silicon material on the wafers, thereby eliminating internal voids in future batches.
With these adjustments, the new batch of microprocessors showed significantly improved internal structural integrity. Ongoing X-ray inspections confirmed that the issue of internal voids had been effectively resolved. This improvement greatly enhanced the performance stability and reliability of the microprocessors, ensuring continuous operational capability in high-load applications.
As a powerful inspection tool, X-ray analysis provides a highly effective quality control method in electronic component manufacturing. It not only ensures product consistency and reliability but also helps manufacturers optimize production processes and reduce defect rates. As technology advances, X-ray analysis is expected to play an increasingly important role in the electronics manufacturing industry, especially in applications demanding high reliability and precision.
Rapid Rabbit, as a leading company focused on electronic component testing and authenticity verification, plays a crucial role. By offering advanced X-ray inspection services, Rapid Rabbit helps manufacturers identify and address potential production issues at an early stage. Rapid Rabbit's services can reveal structural defects on a microscopic scale, such as internal voids or uneven material deposition in wafers, which are often undetectable by conventional methods.