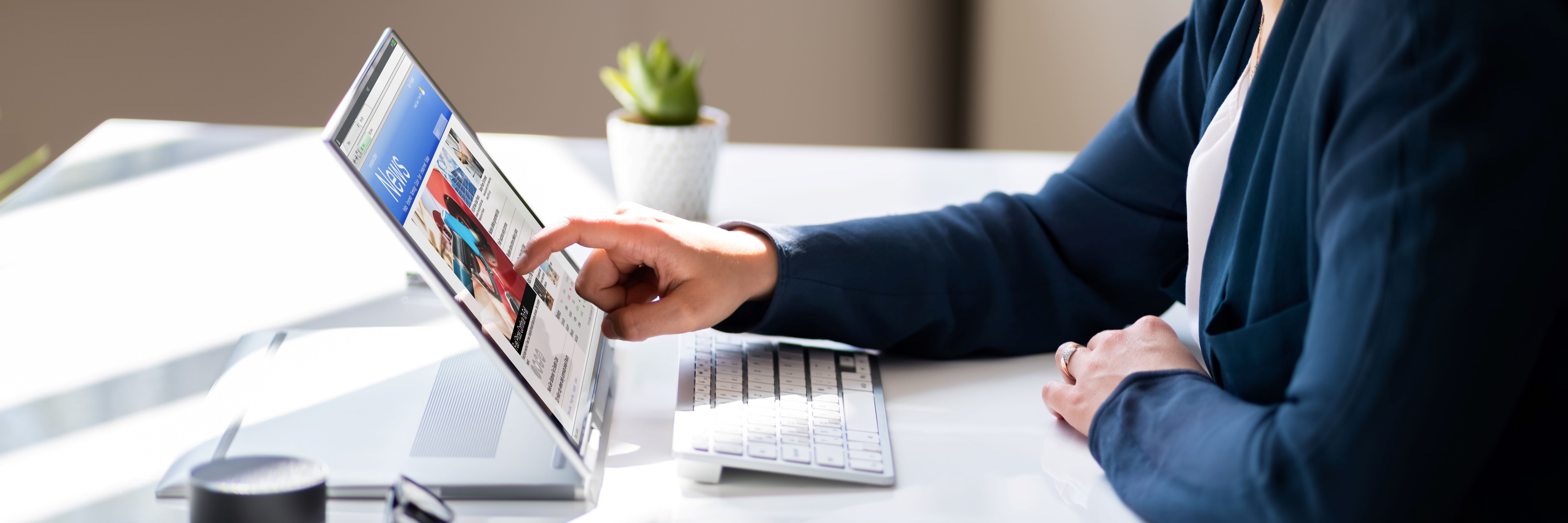
Temperature Sensors
Temperature sensors are widely used across multiple industries such as industrial automation, automotive, aerospace, energy, healthcare, and consumer electronics. They play a crucial role in monitoring and regulating temperature to ensure the stable operation of systems. The reliability of these sensors is especially important in long-term use. To guarantee their stability and accuracy, temperature sensors must undergo strict quality control and reliability testing.
This article will first introduce the basic types and applications of temperature sensors, followed by an in-depth discussion of the reliability testing methods used for these sensors. Additionally, we will explore how these tests optimize product design, improve quality control, and extend sensor lifespan.
1. Basic Concept and Applications of Temperature Sensors
A temperature sensor is a device used to measure temperature changes and convert them into an electrical signal. Based on their operating principles and measurement methods, temperature sensors can be categorized into several main types:
Thermocouples: These sensors measure temperature by generating a voltage difference between two dissimilar metals subjected to a temperature gradient. They are widely used in high-temperature measurement applications.
Resistance Temperature Detectors (RTD): RTDs use the resistance of metal materials (e.g., platinum) that changes with temperature to measure temperature. They are known for their high accuracy and are commonly used in industrial and scientific applications.
Thermistors (NTC/PTC): These sensors measure temperature based on changes in the resistance of materials. They are cost-effective and often used in consumer electronics.
Infrared Temperature Sensors: These sensors measure the infrared radiation emitted by an object to estimate its surface temperature. They are ideal for non-contact temperature measurement.
These sensors are used in various automated control systems, automotive electronics, aerospace, home appliances, medical devices, and other fields. Due to their sensitivity to environmental changes, the long-term reliability of temperature sensors directly affects the safety and performance of equipment.
2. Overview of Temperature Sensor Reliability Testing
The purpose of temperature sensor reliability testing is to simulate the sensor's performance in different operating environments and ensure it can maintain accuracy and stability over time. Below are several common directions for reliability testing of temperature sensors:
Temperature Sensor Parameter Testing:The objective of parameter testing is to evaluate the sensor's performance under different working conditions, ensuring its accuracy, stability, and reliability. The following are some common areas of parameter testing for temperature sensors:
Accuracy Testing: Accuracy is one of the most critical performance indicators for temperature sensors. By comparing the sensor’s output signal with the actual temperature, accuracy testing evaluates the sensor's measurement precision. Common methods include zero offset, full-scale offset, and linearity tests to ensure the sensor provides accurate readings across its entire range.
Response Time Testing: Response time refers to the time delay between a temperature change and the sensor's corresponding output change. Response time testing helps assess how quickly the sensor reacts to temperature variations, which is essential in environments with rapid temperature fluctuations.
Stability Testing: Stability testing aims to evaluate the sensor's output fluctuation and drift over long-term use. By performing continuous measurements over an extended period, engineers can ensure the sensor’s performance remains stable without significant degradation under varying conditions.
Repeatability Testing: Repeatability testing is used to verify the consistency of the sensor's output under the same temperature conditions. This test ensures that the sensor provides consistent measurements each time, improving its overall reliability.
Environmental Resistance Testing: Temperature sensors often operate in extreme environments, such as high temperatures, humidity, or cold conditions. Environmental resistance testing exposes the sensor to these harsh conditions to evaluate its performance and assess how factors like high temperatures, low temperatures, and humidity affect its accuracy.
3. Optimizing Product Design and Quality Control
Reliability testing is not only used to evaluate product durability and stability but also provides valuable data that helps optimize product design, improve manufacturing processes, and enhance quality control. Based on testing feedback, manufacturers can make improvements in several areas:
Material Selection: Testing results reveal the aging trends of materials under extreme conditions, enabling research teams to select materials that are more resistant to high temperatures and corrosion, thus extending the sensor’s lifespan.
Packaging Design: By testing the sensor's performance under humidity, chemical exposure, and other factors, manufacturers can refine the sensor's packaging design, improving its resistance to external environmental influences.
Manufacturing Processes: Test data can also help identify issues in the manufacturing process, leading to improvements in soldering, sealing, and other production steps to enhance product consistency and reliability.
4. Future Trends and Challenges
With the continuous advancement of technology, temperature sensors are evolving in design and application. Below are some major technological trends and future challenges:
Smart and IoT Integration: With the rise of the Internet of Things (IoT), temperature sensors are increasingly being integrated with smart devices for remote monitoring and data analysis. These intelligent sensors not only provide more accurate temperature readings but also feature self-diagnostic functions to predict potential faults and maintenance needs, improving equipment reliability and management efficiency.
Miniaturization and Integration: Modern temperature sensors are moving towards miniaturization and integration. Micro-sized sensors provide accurate temperature measurements in applications with limited space, such as wearable devices and embedded systems. Integrated technologies allow multiple sensors to work collaboratively on the same chip, enhancing device functionality and cost-effectiveness.
Enhanced Environmental Resistance and Long-Term Stability: In specialized applications (e.g., deep-sea exploration and aerospace), temperature sensors must withstand extreme temperature, pressure, and radiation conditions. Developing sensors with high environmental resistance is a major challenge for future advancements, requiring new materials and advanced manufacturing techniques to ensure stable performance in harsh environments.
Low Power Consumption and Energy Harvesting: In IoT and wireless sensor networks, low-power temperature sensors are becoming a key demand. These sensors reduce maintenance costs by extending battery life, particularly in remote monitoring and automation applications. Additionally, energy harvesting technologies, such as thermoelectric generation, are providing new solutions for low-power temperature sensors.
The reliability of temperature sensors is essential to ensure their stable operation in real-world applications. Through systematic parameter testing, manufacturers can evaluate the sensor's performance in various complex environments, identify potential issues early, and use the test data to optimize product design and manufacturing processes. With ongoing technological progress, the reliability testing methods for temperature sensors will become increasingly refined, helping industries offer more reliable temperature monitoring solutions.
Innovations in smart functionality, miniaturization, enhanced environmental resistance, and low power consumption will drive the widespread adoption of temperature sensors across more applications, improving the efficiency and sustainability of industries. In particular, with advanced technologies in place, Rapid Rabbit, as a leading electronic component testing laboratory, offers high-precision testing services that further enhance the reliability of temperature sensors, ensuring their optimal performance in challenging environments. This will assist manufacturers in achieving higher accuracy, stability, and long-term reliability in the development phase, providing a solid technical foundation for future industrial applications and intelligent systems.