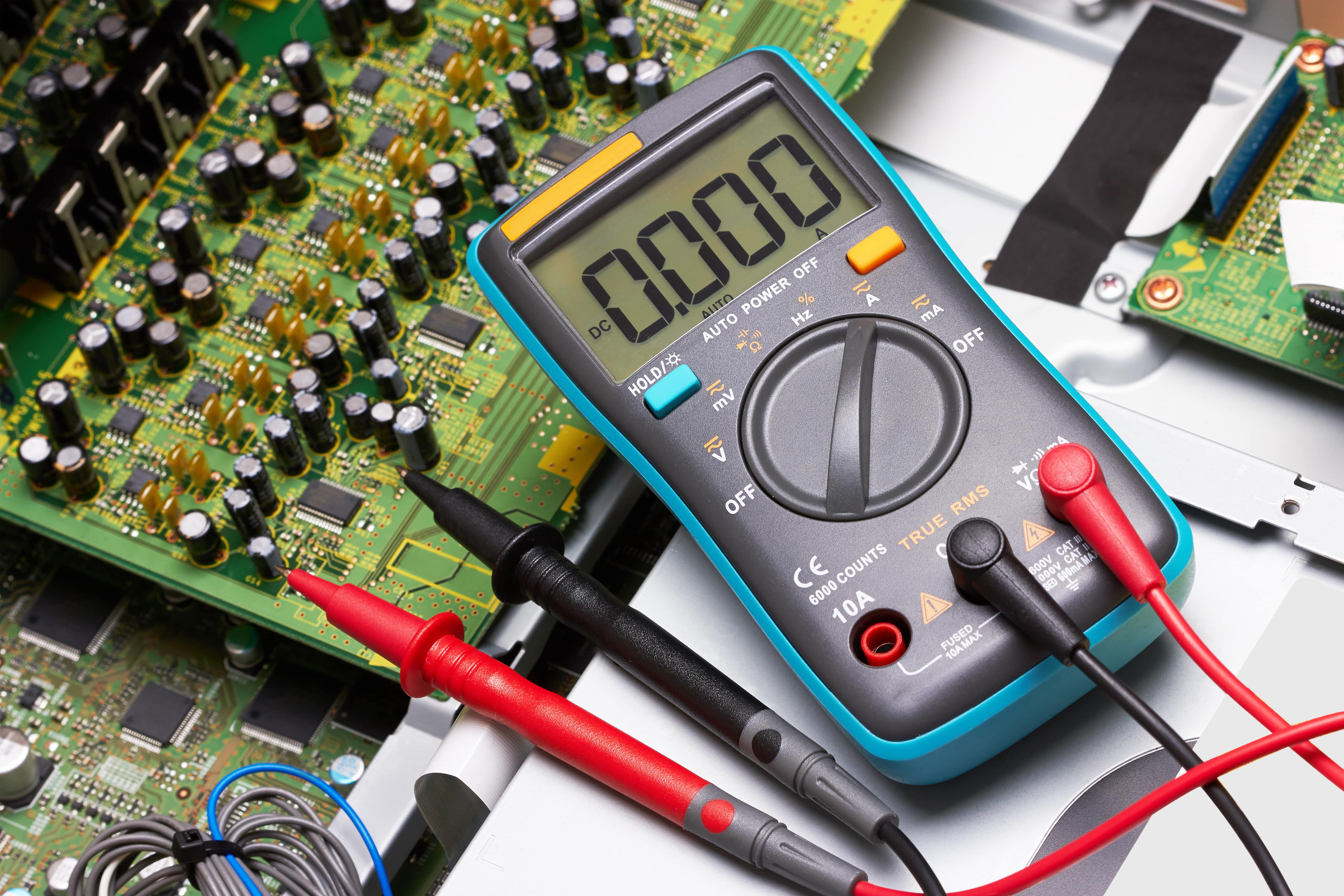
Passive Components Testing Services
Passive components such as resistors, capacitors, and inductors form the backbone of modern electronic circuits and are extensively used across various electronic devices. To ensure the performance and reliability of these passive components, comprehensive testing services provide detailed electrical characteristics and environmental tolerance assessments, ensuring their stability and efficiency in various applications. These tests are widely applied in electronic manufacturing, communication equipment, automotive electronics, and high-reliability application fields.
Basic Principles and Importance of Passive Components Testing
Passive components testing involves measuring key electrical parameters such as resistance, capacitance, inductance, Q factor, Equivalent Series Resistance (ESR), insulation resistance, and Self-Resonant Frequency (SRF) to assess their performance and reliability. Environmental tolerance tests include high temperature, high humidity, vibration, shock, and temperature cycling to ensure component stability under different working conditions.
The performance and reliability of passive components are crucial for the overall quality of electronic devices. Detailed testing ensures these components meet design specifications and application requirements, preventing system failures and performance degradation due to component faults. In high-reliability applications such as aerospace, military, and medical devices, passive components testing provides vital quality assurance, ensuring product stability and performance in harsh environments.
Passive Components Testing Process
Test Preparation:
● Define testing objectives and requirements, select suitable testing equipment and parameters.
● Prepare test samples, ensuring they are undamaged and clearly labeled to obtain optimal test results.
Electrical Characteristics Testing:
● Measure resistance using a high-precision ohmmeter to ensure values are within specification.
● Measure capacitance with precision capacitance measuring equipment to ensure values are within specification.
● Measure inductance using a high-precision inductance meter to ensure values are within specification.
● Measure Q factor and ESR to evaluate the component's quality factor and equivalent series resistance, ensuring performance within the operational frequency range.
● Measure insulation resistance at specified voltages to assess the component’s insulation performance.
● Measure Self-Resonant Frequency (SRF) to determine the performance limits of components in high-frequency applications.
Environmental Tolerance Testing:
● High temperature and humidity testing: Long-term testing of components in high temperature and humidity environments to assess their reliability and durability.
● Vibration and shock testing: Simulating mechanical stress encountered during transport and use to ensure component mechanical stability.
● Temperature cycling testing: Repeatedly heating and cooling components to assess their performance stability under temperature changes.
Data Collection and Analysis:
● Use testing instruments to collect performance data of components under various conditions.
● Use professional software to process and analyze test data, generating detailed performance charts and reports.
Report Compilation and Result Interpretation:
● Document test results in detail, including electrical characteristics and environmental tolerance test results.
● Prepare comprehensive passive components testing reports for subsequent design validation and quality control reference.
Passive Components Testing Equipment
● High-Precision Ohmmeter: Used to measure resistance values, ensuring they are within specification.
● Precision Capacitance Meter: Used to measure capacitance values, ensuring they are within specification.
● High-Precision Inductance Meter: Used to measure inductance values, ensuring they are within specification.
● Q Factor and ESR Meter: Used to evaluate the component's quality factor and equivalent series resistance.
● Insulation Resistance Tester: Used to measure the component's insulation resistance, assessing its insulation performance.
● Self-Resonant Frequency (SRF) Tester: Used to determine the performance limits of components in high-frequency applications.
● Thermal Testing Equipment and Environmental Simulators: Used to simulate high temperature, high humidity, and other extreme cnditions, assessing component reliability.
● Professional Analysis Software: Used to process and analyze test data, generating performance charts and test reports.
In our laboratory, passive components testing is a vital tool to ensure component performance and reliability. By using advanced testing equipment and techniques, we provide our clients with precise, comprehensive component performance analyses. This not only helps clients identify and avoid potentially defective components but also enhances the overall reliability and market competitiveness of their products. Our passive components testing services ensure that clients can confidently select and use the highest quality passive components, thereby achieving higher product performance and safety.